At DiZNEW, we take denim seriously — because quality is in the details. From fabric selection to stitching and washing, every step matters. That’s why we’re your trusted denim apparel production partner in China.

Why Quality Matters?
Product quality is the foundation of customer satisfaction and brand reputation. It significantly influences consumer trust and loyalty, distinguishing a brand in a competitive market. This brief discussion underscores the critical role of quality in ensuring customer retention and building a positive brand image.
The Cost of Poor Quality
Poor quality comes with high costs, including defects that lead to product returns, increased customer dissatisfaction, and ultimately, damage to the brand’s reputation. Highlighting the tangible and intangible losses associated with inferior quality products, this section emphasizes the direct impact of quality issues on a company’s bottom line and market standing.
How We Inspect Your Denim Garments
Whether you choose our Pro or Basic production plan, DiZNEW follows a rigorous inspection process that aligns with international apparel standards — ensuring every denim piece we produce meets your expectations in both form and function.
1. Pre-Production Check:We review fabric, trims, patterns, and sizing to match approved specs.
2. In-Line Inspection (During Production):Our quality control teams monitor manufacturing processes, conducting spot checks and addressing any issues in real-time to prevent defects.
3. Final Random Inspection (FRI):We follow the AQL 2.5 standard for denim garments, inspecting random samples for seam durability, sizing accuracy, wash consistency, fabric flaws, and branding details like labels and patches — only pieces that meet all criteria are cleared for delivery.
4. Packaging and Labeling Review:We inspect the packaging and labeling to ensure it meets legal requirements and is ready for shipment.
5. Loading Supervision (Optional): If needed, our team can supervise the loading process to ensure accurate quantities, proper carton labeling, and careful handling, minimizing damage during transit.
By implementing this comprehensive inspection strategy, we ensure that only high-quality products are delivered, maintaining the integrity of your brand and customer satisfaction.

When you choose our Pro Plan and work with our DiZNEW factory for ODM production, we stand by the quality.
If defects are found during our warehouse inspection, we’ll replace the items at no cost.
If you discover issues within 15 days of receiving the goods and provide evidence, we’ll offer replacements or compensation — guaranteed.
How It Works?
Step-by-Step Guide: Our quality assurance services are designed to be easily accessible and effective, ensuring your products meet the highest standards of quality
1.Contact Us – Reach out via website, email, or phone to book a consultation at your convenience.
2.Custom Plan – We’ll assess your needs and tailor a quality assurance plan specific to your denim product line.
3.Setup & Agreement – Finalize the plan details, then we handle the setup so you’re ready to go.
4.Quality Control Execution – Our team applies inspection protocols to your selected styles or production stages.
4.Reporting – You’ll receive clear reports and improvement suggestions to help maintain consistent product quality.
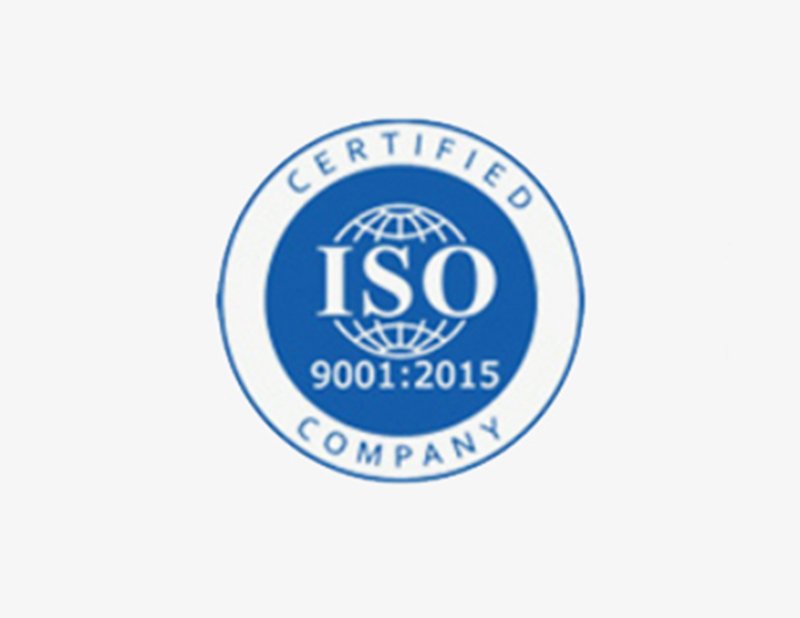
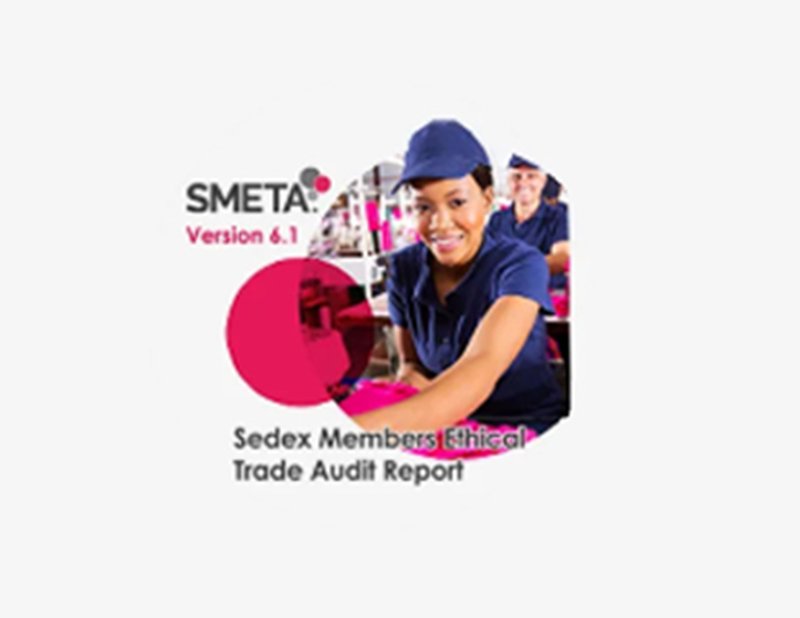
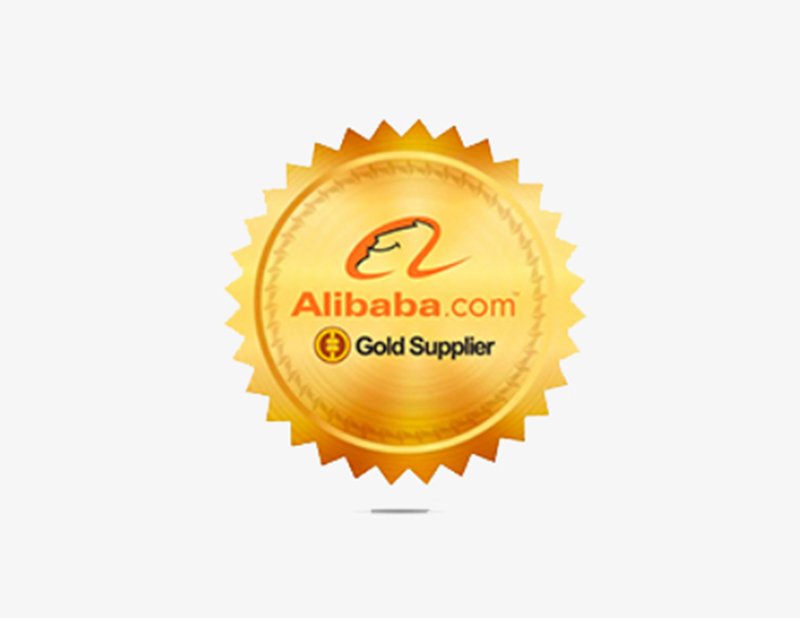
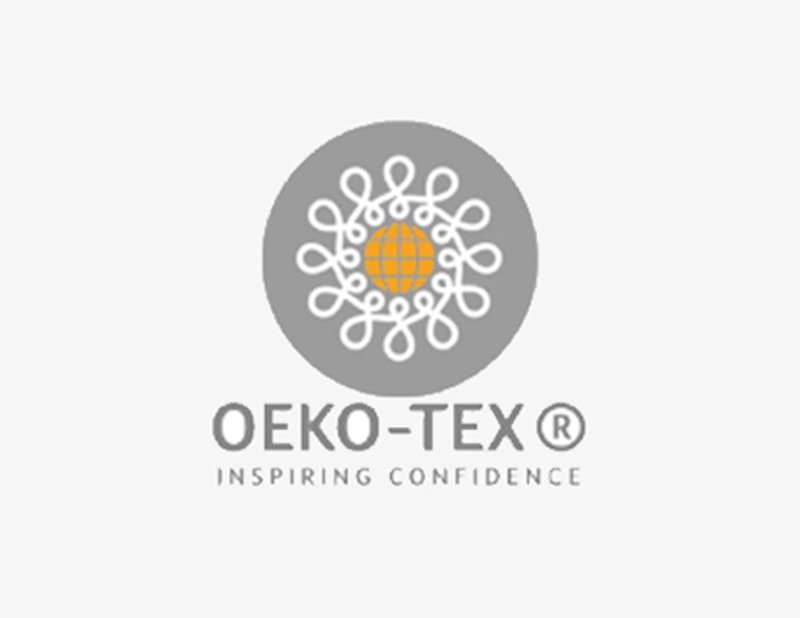
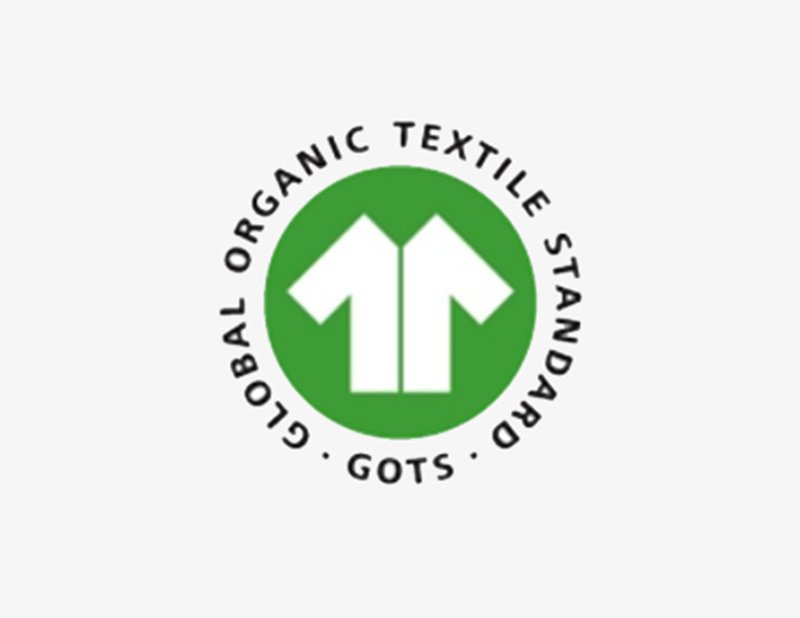
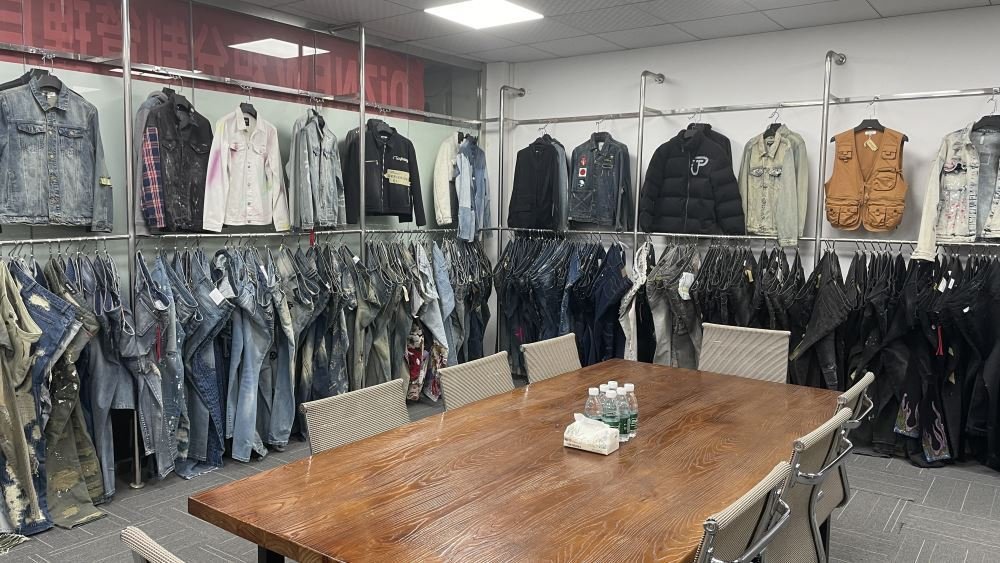
We're Ready To Collaborate With You
If you have any questions or need a quote, please leave us a message. Our Team will respond within 24 hours to assist you in selecting the ideal fashion products tailored to your needs.